ORGANOGRAM
TOP MANAGEMENT
Mohammad Karim Uddin, Deputy Managing Director is a seasoned professional with an extensive 28 years career in the ship recycling industry, demonstrating an in-depth understanding of the nuances and challenges of this sector. His expertise spans ship purchase, recycling management, sales and other key facets of this dynamic sector. His exceptional sales skills honed through years of experience, including effective client relationship management and sales strategies.
As one of the owners of KSRF, he has contributed significantly to its growth and success. His commitment to safety, environmental responsibility and client satisfaction have been the cornerstone of his career, leading to successful outcomes and lasting industry relationships. He is dedicated to furthering the success of the ship recycling industry and is always open to new opportunities and collaborations.
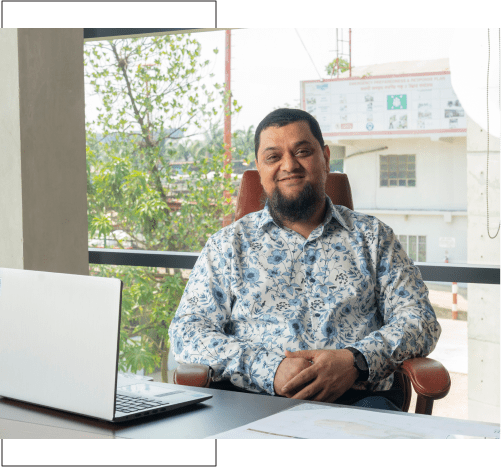
Mohammad Karim Uddin
Deputy Managing Director
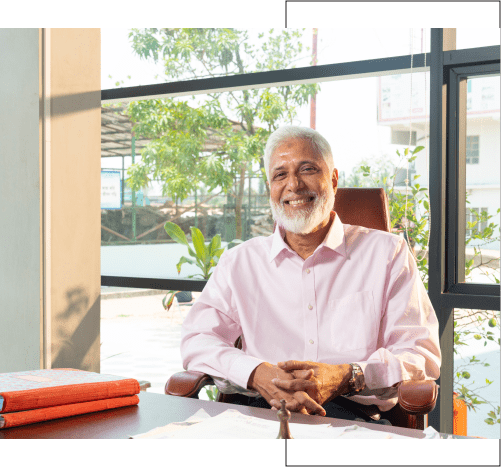
M A Karim
Director, Operation
Abdul Karim Dulal is a highly experienced Director with a remarkable career spanning more than 35 years in the ship recycling industry of Bangladesh. Mr. Dulal has been at the forefront of leading production efforts in ship recycling yards, ensuring efficiency and adherence to safety and environmental standards. His profound knowledge and skills in material segregation have contributed to the efficient extraction and processing of valuable materials from scrap vessels.
Mr. Dulal has a successful track record in the sales of equipment and various types of non-ferrous materials, further adding value to the ship recycling process. Over the years, he has witnessed and actively influenced the transformation of the ship recycling industry in Bangladesh, demonstrating a forward-thinking approach and adaptability to industry changes. Abdul Karim Dulal’s extensive experience, leadership and commitment to excellence have solidified his reputation as a respected figure in the ship recycling sector and he continues to contribute significantly to its growth and sustainability.
Mohd. Mehrul Karim, CEO is a highly accomplished maritime professional with an extensive career spanning over four decades. With a background as a Class-1 marine engineer and an MBA degree, He has held various significant roles in the maritime industry, showcasing his exceptional knowledge, leadership, and expertise. His extensive expertise includes serving as a Class Surveyor and Deputy Country Manager at Germanischer Lloyd. As a Lead Auditor for ISM, ISPS and MLC, Mr. Karim demonstrated his commitment to the highest standards of safety, security and labor regulations in the maritime sector. Furthermore, he holds the distinction of being a DNV approved Hazmat expert.
Notably, Mr. Karim has made significant contributions to the shipbuilding industry in Bangladesh and is renowned for his proficiency in safety and environmental regulations within both the maritime and ship recycling sectors. Currently, he also leads SR Shipping, the largest shipping lines in Bangladesh, overseeing a substantial fleet of 23 supramax bulk carriers.
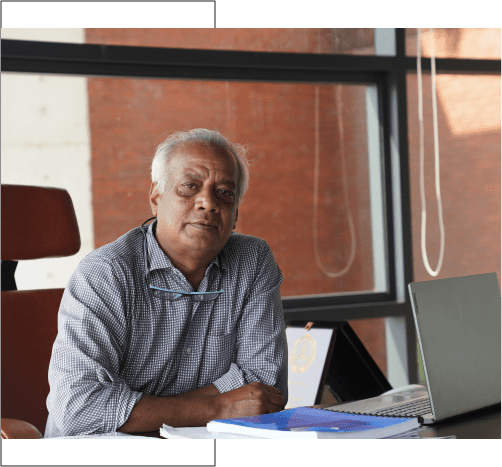
Mohd. Mehrul Karim
CEO & HAZMAT EXPERT

Md. Al Amin
Facility Coordinator & Naval Architect
Md. Al Amin is a distinguished Naval Architect with a wealth of experience across the maritime industry. With a career spanning various roles in ship design, shipbuilding, marine surveying and management system certification, he has emerged as a well-rounded professional in his field.
Having graduated with a degree in Naval Architecture & Marine Engineering from BUET in 2009, Md. Al Amin embarked on his journey as a ship designer at Ananda Shipyard and Slipways Limited. He later honed his skills further at Khulna Shipyard Limited, where he gained valuable insights into ship design.
In 2011, he transitioned into the realm of marine surveying, working with renowned classification societies Germanischer Lloyd and DNV-GL. Through these experiences, he gained exposure to top-notch shipbuilding practices from South Korea’s leading shipyards (DSME & SAMSUNG) and specialized knowledge in shipbuilding materials and welding techniques from Germany.
Md. Al Amin’s career trajectory then shifted towards Management System Certification. He assumed roles as a Lead Auditor and Trainer for Quality (ISO 9001), Environment (ISO 14001) and Health & Safety Management Systems (ISO 45001). Notably, he served as the Business Development Manager & Country Representative of DNV-GL Business Assurance in Bangladesh. His contributions extended across diverse industries, including shipbuilding, ship recycling, steel, RMG, paint & chemical and maritime education.
Presently, Md. Al Amin holds the position of Facility Coordinator at Kabir Ship Recycling Facilities. In this capacity, he spearheads the development, implementation and oversight of ship recycling activities aligned with the Hong Kong International Convention for safe & environmentally sound ship recycling.
Partha S. Guha is a highly skilled and experienced marine engineer with over three decades of dedicated service in the maritime sector. He holds a competency certificate from the United Kingdom, demonstrating his proficiency and expertise in various aspects of marine engineering.
With a strong background in safety and compliance, Partha has also served as an internal auditor certified under ISO 45001 standards. His commitment to professional development is evident through his participation in training programs such as the SENSREC project’s Training of Trainers (ToT) initiative and completing a course on IHM (Inventory of Hazardous Materials) & SRP (Ship Recycling Plan) awareness. Currently, Partha is a valuable member of Kabir Ship Recycling Facilities team, working as Technical Coordinator and contributing his knowledge and experience to the organization for the past seven years.
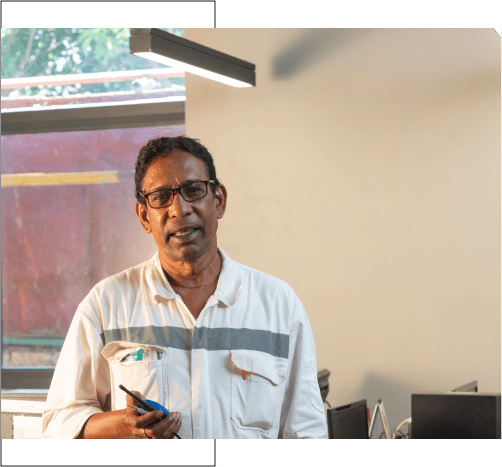
Partho S. GUHA
TECHNICAL COORDINATOR
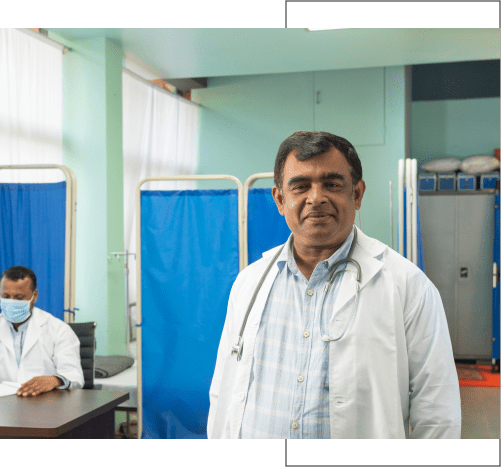
Dr. Mesbah Uddin
MEDICAL CONSULTANT
Dr. Mesbah Uddin is a highly experienced medical professional with a strong background in occupational health and safety. With a MBBS degree from Chattogram Medical College and specialized training in diabetes management from BIRDEM, Dhaka, he has dedicated his career to ensuring the well-being of industrial workers. Dr. Mesbah has lent his expertise to various industries including Unilever, Heidelberg Cement, Western Marine Services, Ispahani Group and A & A Textile, where he has effectively addressed worker’s occupational health issues.
In addition to his role as a part-time medical consultant at the Bangladesh Shipping Corporation and Mutual Trust Bank, Dr. Mesbah has been actively involved in Kabir Ship Recycling Facilities since 2010, where he continues to contribute his valuable insights and medical knowledge to promote worker safety and health.
His areas of expertise encompass workers’ health, safety protocols, emergency response coordination and the management of trauma and burn patients. Dr. Mesbah Uddin’s dedication to improving the well-being of industrial workers and his extensive experience make him an invaluable asset in the field of occupational health and safety in Bangladesh.
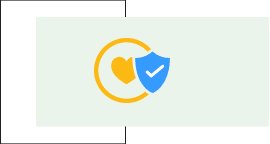
Occupational health & safety management
- Facility has established employee Health Base Line.
- At the intake stage each employee is screened for their health condition and those who meet the requirement are only employed.
- The Facility ensures regular Medical Check Up for all employees considering the occupational health risk assessment.
- Those who directly exposed to HazMat and Cutting Process are additionally checked for Lung Function as Company Medical Officer’s advice.
- The facility has first-aid kits to respond to injuries or exposure to Hazardous Materials.
- Provide appropriate PPEs for all employees following the PPE matrix.
- The facility has proper Medical Facility for emergency and initial medical management
-Medical Centre
-MBBS Doctor
-Full Time Paramedics
-Own ambulance
- The facility secured the availability of heath care facilities and hospital within a reasonable distance when further medical treatment and care is necessary.
- State of the art Negative Pressure Unit (NPU) with designated PPEs for ACM Handling.
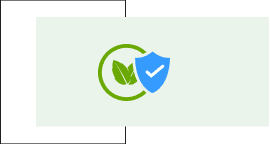
Environment Management
Kabir Ship Recycling Facilities are committed to recycle the ship in an environmentally sound way:
- Comply with Integrated Management System, Applicable Legislation, Regulations and another requirement.
- Developed own methodology for environmental aspect impact analysis of individual activities
- Regular monitoring of ambient air, exhaust gas, soil, water, sound etc.
- Maintaining large water body (pond) inside the facility
- Tree plantation inside the yard
- Special dust collection car
- Regular water spray to minimize the dust
- Dedicated oily block handling process comprises of
-Oily block handling tray
-Over the ground oily water holding and separation tank
-Oily water separator capable to separate the heavy metal as well
-Incinerator for burning the oily rugs
Hazmat Management
Management of Hazardous Materials:
The Facility has adequate space for individual types of hazmat and ensure the proper management of all Hazardous Materials by following below:
- IHM is prepared for individual ship by hazmat expert:
-Marking of Hazmat on board by Hazmat Expert
-Hazmat sample collection for laboratory test
-IHM is prepared by independent third party
-Items from IHM Part-III are used in running vessel of our sister concern
- All hazardous materials as well as wastes generated during the ship recycling process are handled, separated, transported and stored only in safe containers / containments and / or on impermeable floors with effective drainage systems.
- Whenever hazardous wastes or materials containing such wastes are separated from the ship, contact with unprotected soil or the sea is prevented.
- Oily block cleaning tray, oily water separator tank and OWS are used to handle the oily block.
- All the hazardous material are segregated properly and stored in the designated storage as marked.
- For glass wool, SRF use the bale compactor machine for compacting the wool and then stored in designated area.
- For ACM handling, SRF has Negative Pressure Unit (NPU) (Decontamination Unit) in yard and also has portable NPU to handle the ACM on board.
- The hazardous waste are handed over to the only Govt. approved hazmat handler.
- Other hazmat are stored inside the facility until the Govt. TSDF is in operation.
- Ship Specific Hazmat Management Record
- Each hazmat is tracked by following in house tracking system
- Transport emergency card is used for the transportation of hazardous material
Quality Management
At Kabir Ship Recycling Facilities, quality is at the heart of everything we do. We take pride in our commitment to recycle the vessels and delivering products & services that not only meet but exceed our stake holders (ship owner, authorities, safety agencies, customers, NGOs, media partners etc.) expectations. Our Quality Management System is the cornerstone of our dedication to quality and it guides every aspect of our operations.
Our Commitment to Quality:
- Stake Holder’s -Centric Approach: We put all our relevant stake holders at the forefront of our QMS. Understanding their needs, expectations and feedback is crucial to recycling the vessels in a safe and environmentally sound manner.
- Quality Policy: Our Integrated Ship Recycling Policy outlines our commitment to quality, our objectives and the principles that guide our actions. It is communicated and understood at all levels of our organization.
- Continual Improvement: We have a culture of continual improvement. We consistently review and enhance our processes to ensure that we are always striving for higher quality standards.
Key Elements of Our QMS:
- Documented Procedures: We have clearly documented procedures for every critical process within our organization. These procedures serve as a reference point to ensure consistency and quality in our operations.
- Risk Management: Our QMS includes robust risk management processes to identify and mitigate potential issues before they impact our operations.
- Employee Training: We invest in the development of our employees through training programs that enhance their skills and understanding of quality standards.
- Performance Metrics: We set and monitor key performance indicators (KPIs) to assess the effectiveness of our QMS and identify areas for improvement.
- Vendors and Partner Engagement: We work closely with our vendors, suppliers and partners to ensure they meet our quality standards, fostering a shared commitment to quality throughout our supply chain.
- Regulatory Compliance: Our QMS ensures that we comply with all relevant laws, regulations and industry standards, providing peace of mind to our customers.
- Feedback and Improvement: We actively solicit and act upon customer & employee feedback, using it to drive improvements in our products and services.
- QMS Control Hierarchy: Our dedication lies in adhering to the following control hierarchy during the implementation of our quality management system within our facilities.